Kaum ein Verbraucher ist sich des Know-hows und der Komplexität bewusst, die in einem scheinbar einfachen Kunststoffdeckel oder einem Verschluss einer Getränkeflasche stecken. Dabei kommt gerade diesem Teil einer Verpackung eine zentrale Rolle zu.
Diese ist hauptsächlich funktional: Verschlüsse müssen dicht sein und es auch bleiben, sie müssen zugleich leicht zu öffnen sein und sichtbar machen, ob sie schon einmal geöffnet wurden. Sie müssen Drücke aushalten oder einen Fall aus dem Regal. Bei all dem sollen sie aber auch noch zu niedrigen Kosten herstellbar sein und gut aussehen. Da braucht es schon einen Spezialisten, um all diese Anforderungen zu erfüllen, und zu den führenden Spezialisten auf diesem Gebiet gehört United Caps. Das Unternehmen ist insbesondere in Europa und Asien als Anbieter von innovativen Deckeln und Verschlusssystemen für die Lebensmittel- und Getränkeindustrie sowie für Agrarchemikalien bekannt und feierte 2019 sein 80-jähriges Bestehen.
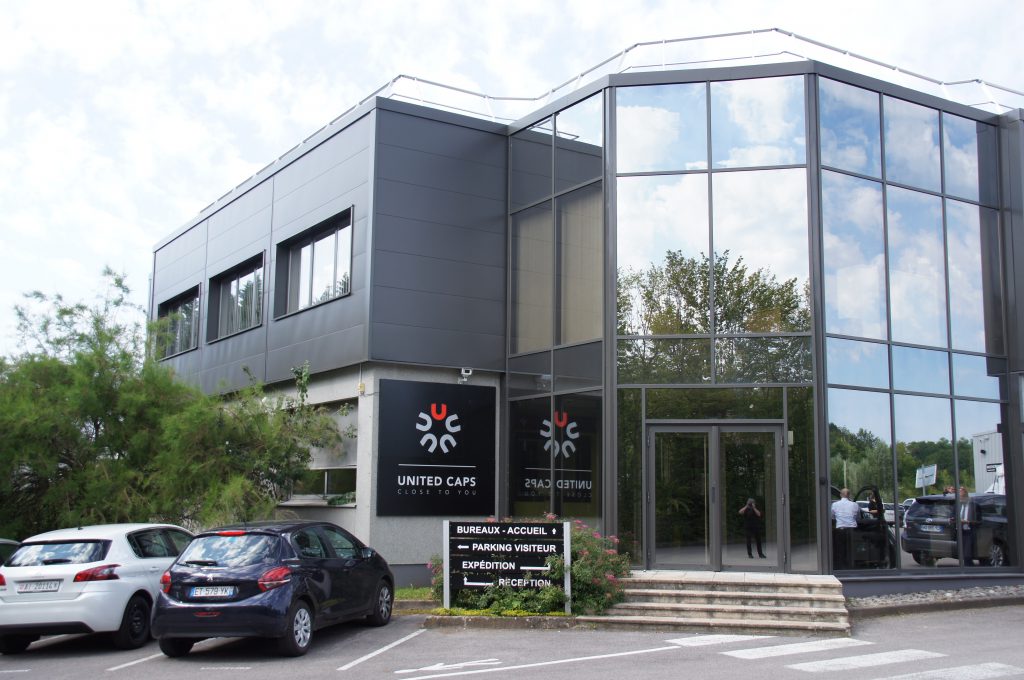
In gut der Hälfte der Fälle handelt es sich bei den Produkten von United Caps um maßgeschneiderte Lösungen, die nicht nur speziell auf den Bedarf eines Kunden abgestimmt sind, sondern auch in enger Zusammenarbeit zwischen dem Kunden und dem Forschungs- und Entwicklungszentrum von United Caps entstehen. Ein Beispiel dafür ist der Verschluss für die Nescafé-Gold-Gläser, die seit Mitte 2018 im Handel sind: Hersteller Nestlé wollte für seine Instant-Kaffee-Produktserie eine elegante Verpackung schaffen, die dem Markttrend bei Kaffeeprodukten zum Premium-Image folgen sollte. Dafür suchte das Unternehmen nach einer Möglichkeit, dem im Spritzgussverfahren hergestellten Kunststoffverschluss einen edlen Metall-Look mit gebürsteter Oberfläche zu geben und wandte sich 2015 damit an United Caps.
Die Spezialisten bei United Caps erwogen eine Lösung im In-Mould-Labelling (IML)-Verfahren, ohne sicher sein zu können, dass metallisiertes IML überhaupt realisierbar war – immerhin hatte das bis dahin noch nie jemand gemacht. Man unterbreitete Nestlé unter dem Hinweis auf die notwendigen Entwicklungsanstrengungen ein Angebot und schloss im Oktober 2015 eine entsprechende Vereinbarung mit dem Hersteller.
„Geht nicht“ gibt´s nicht
Auf die Forschungs- und Entwicklungsabteilung von United Caps in Messia kamen drei Problemstellungen zu, deren Überwindung bisher als unmöglich galt: Erstens sollte ein Metall-Look mit gebürsteter Oberfläche bei einem 100 Prozent metallisierten IML-Etikett realisiert werden – trotz aller Bedenken seitens der Etikettenhersteller bezüglich elektrostatischer Wechselwirkungen in der Spritzgussform. Zweitens sollte der Effekt einer gebürsteten Oberfläche mit Hilfe einer Gravur auf dem Deckelrand erzeugt werden, die sich in das Etikett überträgt. Sie musste also Teil der Spritzgussform sein, durfte aber die Entnahme der Verschlüsse aus der Form nicht beeinträchtigen. Damit dies überhaupt möglich war, musste der Deckelrand möglichst unauffällig leicht konisch sein – hier bewegte man sich an der Grenze der möglichen Gravurtiefe.
Erfahrungen, auf die man zurückgreifen konnte, gab es nicht: Dieser Deckel würde das erste Produkt seiner Art auf dem Markt mit einem IML-Etikett auf der Seite sein. Drittens sollte am Deckel keine Nahtstelle sichtbar sein, also musste das IML-Etikett überlappend angebracht werden. Überhaupt war die präzise Platzierung des Etiketts eine zentrale Bedingung, denn es reicht exakt bis zum Rand des Deckels. Eine vierte, nicht ganz so unmögliche Herausforderung kam noch hinzu: Der metallische Look durfte nicht so leicht durch Kratzer oder andere mechanische Einwirkungen zerstört werden, also musste die Oberfläche durch eine Laminierung geschützt werden. Und der fünfte Faktor war der Zeitdruck: Nestlé hatte einen nicht verschiebbaren Termin vorgegeben, an dem sein Werk in Großbritannien mit der Produktion beginnen musste.
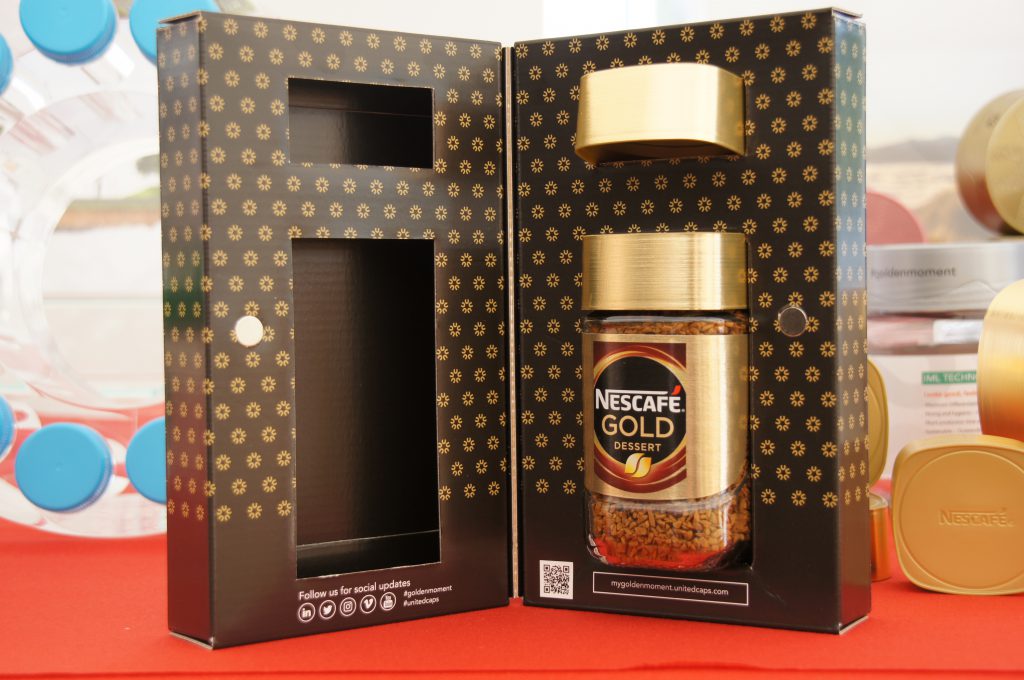
Dass dieses technisch ebenso wie zeitlich ambitionierte Projekt zur allseitigen Zufriedenheit innerhalb von nur zwei Jahren zur Produktionsreife gebracht werden konnte, war auch der Erweiterung der Forschungs- und Entwicklungsabteilung von United Caps am Standort Messia zu verdanken: Sie wurde flächenmäßig um ein Drittel vergrößert um Platz für weiteres Equipment und entsprechendes Personal zu schaffen. So wurden unter anderem eine spezielle Testanlage zur Simulierung von Kratzern und eine zweite Spritzgussmaschine für die Gravurtests mit IML-Etiketten aufgestellt. Letztere diente auch zur Optimierung der Taktzahl und dem Feintuning des Spritzgussprozesses. Zur weiteren Ausstattung zählen außerdem ein 3D-Drucker, ein spezieller Verschlusstester, von dem es in Europa nur noch einen weiteren gibt, ein hochpräzises, dreidimensionales Messgerät und natürlich eine komplett virtuelle Konstruktion und Simulation, mit der viele Eigenschaften eines Produktes schon vor dem ersten Prototypen getestet werden können.
Ein goldener Moment
Benoit Henckes, CEO von United Caps, betonte anlässlich einer Presseveranstaltung im Jahr 2018 denn auch die strategische Bedeutung der Forschungs- und Entwicklungsabteilung in Messia für sein Unternehmen: „Die Erweiterung unserer Kapazitäten hier ist eine Investition in künftiges Wachstum. Hier werden Visionen zur Realität, hier wird das Unmögliche entwickelt.“ Ausdrücklich lobte er die Mitarbeiter: „Ich möchte an dieser Stelle ein besonderes Lob an das Forschungs- und Entwicklungsteam von United Caps für seine Beharrlichkeit aussprechen. Manch anderer hätte sicher mehrmals im Verlauf des Projekts die Flinte ins Korn geworfen. Das gesamte Projekt dauerte zwei Jahre, wobei die ersten Prototypen in weniger als einem Jahr ausgeliefert wurden.“
Denn die neuen Verschlüsse wurden nicht nur in Messia entwickelt, sondern werden dort auch hergestellt. Die Serienproduktion hielt weitere Herausforderungen bereit: Es wurden zwei spezielle Spritzgussmaschinen mit dem Lieferanten Engel entwickelt, von denen je eine den Innenteil und eine den Außenteil des Verschlusses produziert. Bei der Überprüfung des Fertigungsablaufs stellte sich heraus, dass ein kleines Teil an der Maschine den Durchsatz bremste. Problem erkannt, Problem gebannt: Innerhalb von nur einer Stunde konnte die Produktion um 30.000 Teile pro Tag gesteigert werden. In der Etage über der Spritzgussanlage werden beide Teile mit einer Siegelfolie zusammengeführt. Für den behutsamen Transport der Deckel nach oben wird ein Fördersystem verwendet, wie es auch in italienischen Teigwarenfabriken eingesetzt wird, um die empfindliche Pasta zu transportieren. Insgesamt werden so 50 Millionen Teile pro Jahr hergestellt. Henckes sprach denn auch mit Blick auf die erfolgreiche Kooperation mit Nestlé und natürlich in Anspielung auf die Farbe des Verschlusses von einem „goldenen Moment“.
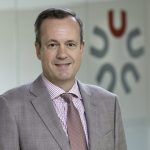
Quelle: United Caps
United Caps hat sein Forschungs- und Entwicklungszentrum in Messia, Frankreich, ausgebaut. Mit den zusätzlichen 200 Quadratmetern Grundfläche umfasst die Anlage nunmehr 600 Quadratmeter. Eine 30-prozentige Personalsteigerung, die Anschaffung eines 3D-Druckers für die Prototypen sowie eine organisatorische Umstrukturierung gingen mit der Flächenvergrößerung einher. Im Schnitt ist nun die Entwicklungszeit zwischen 10 und 20 Prozent geringer – ein wichtiger Faktor für Kunden, um die Entwicklungszyklen für ihre Produkte zu verkürzen.